Table of Content
A general contractor will be familiar with local framing subcontractors; owner-builders can ask other subcontractors on the project for recommendations. Verify that the framing contractor is properly bonded, insured and licensed; and check references. There’s more than one kind of house framing to choose from, although by far the most popular is conventional platform stick framing. We’ve already mentioned steel framing, but a popular wood framing technique is a rigid frame system like timber framing or pole framing . Rigid framing requires fewer – but larger – framing members and is more expensive than platform framing. The cost of framing materials depends on the material you choose, lumber or steel.
For example, let’s say you have hired a contractor with a large fleet of trained house framers or framing contractors and the framing for the exterior walls and interior walls arrives on site pre-assembled. In this scenario, everything might be finished in a couple of days. The type of garage you prefer for your home can influence the cost to frame your house. For example, there will be variable costs included for a detached garage vs attached garages, as well as how many car spaces you need.
House Building Calculator | Estimate Construction Cost
For example, intersecting walls require more studs which increases material costs and labor costs. However, architectural details like slopes and valleys are significantly more difficult, which means more time and higher labor costs. The costs for framing a house include building the stick frames that will become the home's walls.
Wall areas are generally built on the ground or flooring surface area, then raised into their place. Accuracy is essential; in a badly framed finished home the drywall might not be flat, the floorings might squeak and the doors may not close appropriately. This Old Home notes framing ideas, and AskTheBuilder describes roofing system framing essentials.
Garages
You might consider building a tiny home or adding one to your property as a guest house. On average, building a tiny house will cost around $25,000 to $35,000. By converting a shipping container or reusing materials, some homeowners have created tiny homes for less than $10,000. Ranch-style homes tend to cost $100 to $200 per square foot on average. Even though they are one-story, they often cost more than a two-story due to their widespread floorplans and high foundation expense.
A low-priced project would be considered expensive if it wasn’t done correctly or the quality and durability are questionable since you’ll end up having to pay more for repair and reconstruction. Labor – your choice of materials would spell a significant difference in the total labor cost of the project as metal studs would be more expensive to install than wood. The skills and experience of the workers would also play an important role in the costing. If there are a lot of ideas going through your head in the middle of construction, changing anything may not only be annoying having to revise what has been started but also rather costly. No matter how small or trivial you think a simple alteration is, it can oftentimes create a domino effect on the entire project cost to frame a house. A pole barn house completely finished out will cost $30 to $45 per square foot which makes it the cheapest house to build with quality in mind.
BUSINESS SERVICES
This can fluctuate a bit depending on local labor costs and seasonal rates. It should work out to an average total of $15,000 to $30,000 to frame a building. Lumber prices are always fluctuating and can be difficult to predict. This is especially true in today's environment of rising prices. A reasonable estimate for house building lumber costs is somewhere around $15 to $30 per square foot. For an average sized home, this works out to approximately $35,000 to $55,000 (this price also includes the price of nails, etc.).
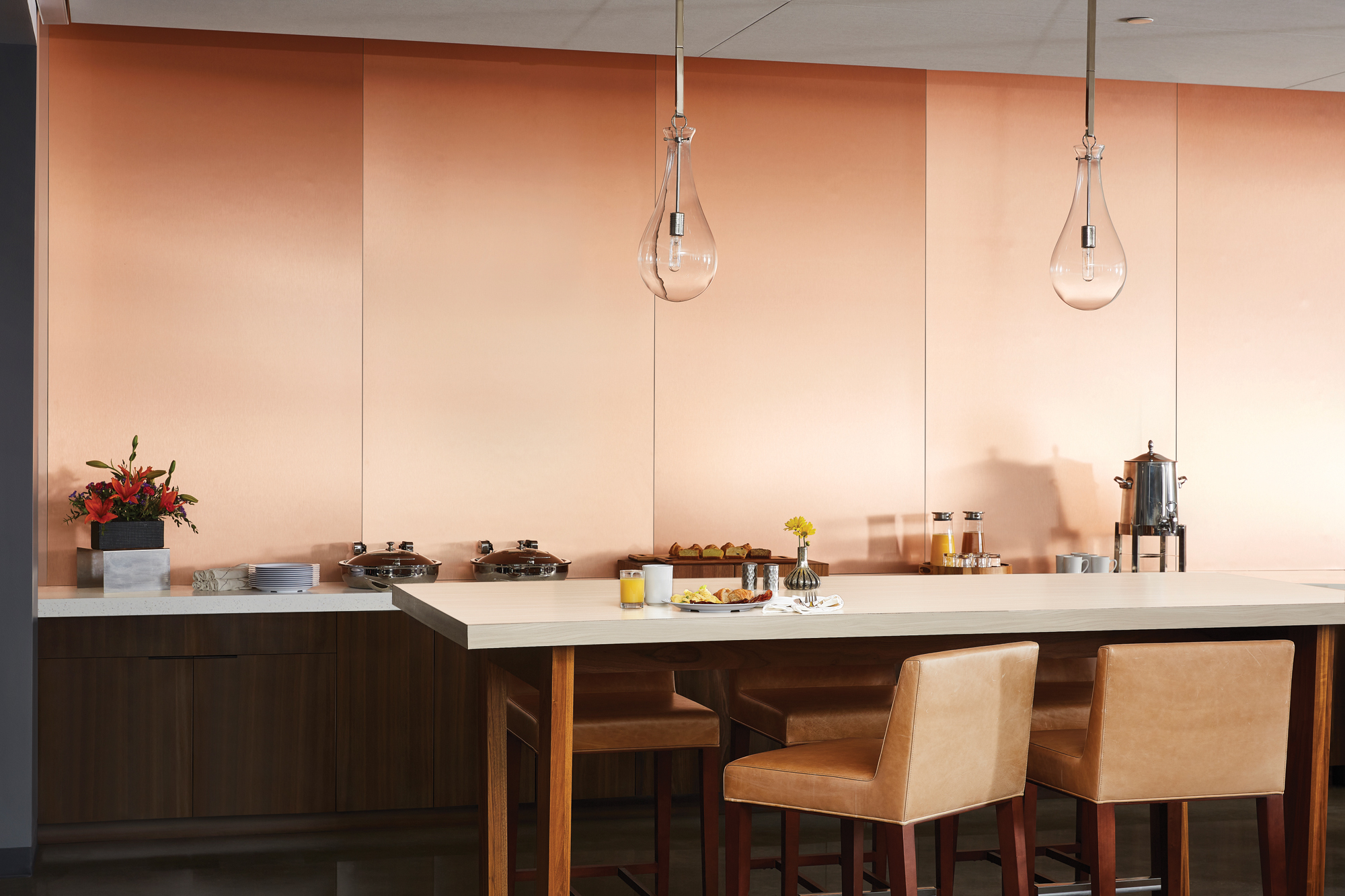
The nation’s overall housing supply remains limited, as those who purchased homes in recent years at extremely low mortgage rates are staying put. This tight inventory has kept prices from seeing deeper declines, making homes still unaffordable for many, especially first-time homebuyers. Surging mortgage rates have put some much-needed pressure on the hot housing market in recent months after home prices hit record highs across the nation.
What are the framing costs per square foot when building a house?
A home’s frame is essentially its skeleton, and it’s crucial to supporting all the other elements. Boost your online presence and work efficiency with our lead management software, targeted local advertising and website services. Showcase your business, get hired and get paid fast with your premium profile, instant invoicing and online payment system. Assume a completely destroyed, 1920 two story vintage home with rough fieldstone, gypsum cement, basement about 26 X 42 Ft. Any estimate as to cost to remove the old basement walls and replace with poured? By comparison, the cost of a prefabricated home is at least 25-35% less than a custom one.
Also available are I-Joists that range from $1.88 to $4.25 per foot and Rim Boards ranging from $16.80 to $29.44 per foot depending on size. Columns, on the other hand, range from $5.26 to $11.98 per foot depending on size and thickness. The 3½” thick ranges from $8.78 to $16.97, the 5¼” thick ranges from $14.90 to $29.09, the 7” thick ranges from $20.06 to $40.63, for the sizes ranging from 9½” to 18″. Solicit bids from 3 to 5 contractors, check their online reviews, make sure they have insurance, and meet with them in person to walk you through their proposals. Once built, you or your contractor will need to schedule a final inspection to obtain a certificate of occupancy.
The frame of a home brings the weight load of the roofing system to the foundation so the whole structure is supported, and offers a weather-tight barrier against natural elements. Framing costs make up around 8-12% of your home addition’s total cost. These costs vary drastically depending on the materials used and the overall design of your addition.
Beach houses require an additional $20,000 to $60,000 on top of your build price to set the pier-and-beam foundation. It’s tempting to build the house now and lift it in the future, but lifting a house can run $25,000 to $100,000. It’s best to build the stilts now and save money in the long run and keep your home safe from flooding in the meantime. Choosing a popular or more standardized floor plan will often be less expensive than a custom design with unique features.
They include the siding, roofing ($5,600–$11,500), exterior painting ($1,800–$4,400) and exterior doors and windows ($3,000–$9,300). Use the cost breakdown below to check bids provided by construction companies. These costs are based on a 2,000 square foot home built at an average cost of $125 per square foot. These prices are averages and will vary depending on the materials used, type of home, and quality of construction. They range from about $10 per square foot to almost double that recently because of the pandemic. The labor costs to frame a home typically run $5 to $10 per square foot.
Some materials may be cheaper now but lead to a higher cost of ownership because of maintenance, energy costs, and replacement costs down the road. You will need to contact a lender and figure out what kind of mortgage you will qualify for. For potential homeowners looking to save money, building your own home costs about $70 per square foot and will save an average of 25%. On a typical home costing $248,000, you would save around $62,000.
Basic Costs to Build a House
The bid set includes all the relevant information your contractor needs, including the floor plan and exterior images or elevations of each side plus roof pitches, to give you a cost-to-build estimate. Your contractor will examine the plans, ask questions, and take notes to get a full picture of your dream home design. The cheapest way to build a house is something that has two data points – the cost now and the cost later. Many materials used in the construction of your home will be available in a variety of qualities and prices.
Shipping container houses take about 30% less time to build than a traditional home. The following costs are related to turning a container into a home. Custom home builders can develop anything you want once you have all the design features in the blueprint. However, your home will cost more purely because they are giving your home their exclusive focus and ordering in materials and hiring workers for one house.